In the realm of dentistry, innovation continues to push boundaries and redefine traditional practices. One such innovation that has garnered considerable attention is the advent of 3D-printed dental implants. Representing a groundbreaking leap forward in implant dentistry, these implants offer unparalleled customization, precision, and potential to revolutionize patient care. In this article, we delve into the world of 3D-printed dental implants, exploring their development, benefits, applications, and future prospects.
The Evolution of new type of dental implants
New type of Dental implants have a rich history that dates back thousands of years, with evidence of rudimentary implant-like devices found in ancient civilizations such as the Mayans and Egyptians.
However, modern dental implants as we know them today have undergone significant evolution and refinement over the past century.
The concept of osseointegration, or the direct bonding of bone to metal, laid the foundation for modern dental implantology. This concept was first introduced by Swedish orthopedic surgeon Dr. Per-Ingvar Brånemark in the 1950s while conducting research on bone healing and regeneration.
Dr. Brånemark accidentally discovered osseointegration when he observed that titanium implants placed in rabbit bone could not be removed without fracturing the bone tissue.
Building on Dr. Brånemark’s groundbreaking work, the first successful human dental implant surgery was performed in 1965 by Dr. Leonard Linkow, an American dentist.
Over the following decades, advancements in materials science, surgical techniques, and implant design further refined the field of implant dentistry.
Traditional dental implants
Is typically made from titanium or titanium alloy, became the standard of care for replacing missing teeth. These implants consist of three main components: the implant fixture, which is surgically placed into the jawbone; the abutment, which connects the implant fixture to the prosthetic tooth or restoration; and the prosthetic tooth or restoration, which is attached to the abutment and resembles a natural tooth.
Also read: The Ultimate Guide to Buying Dental Supplies Online in 2024
Despite their success, traditional dental implants have limitations, particularly in cases of inadequate bone volume or compromised bone quality.
In recent years, technological advancements, such as cone beam computed tomography (CBCT) imaging and computer-aided design/computer-aided manufacturing (CAD/CAM) technology, have enabled more accurate treatment planning and implant placement.
Enter a new type of dental implants 3D-printed dental implants – the latest frontier in implant dentistry. 3D printing technology, also known as additive manufacturing, has revolutionized the fabrication of dental implants by allowing for precise customization and rapid production. With 3D printing, dental professionals can design implants tailored to each patient’s unique oral anatomy, resulting in better fit, function, and aesthetics.
Overall, the evolution of new type of dental implants from primitive prototypes to sophisticated 3D-printed constructs reflects the relentless pursuit of innovation and excellence in implant dentistry.
As technology continues to advance and our understanding of biomaterials and tissue engineering deepens, the future of dental implants holds even greater promise for improving patient care and transforming smiles around the world.
Understanding 3D Printing new type of dental implants in Dentistry
3D printing, also known as additive manufacturing, has emerged as a game-changing technology in dentistry, offering unprecedented levels of customization, precision, and efficiency in the fabrication of dental prostheses, surgical guides, and implants. Here’s a closer look at how 3D printing is revolutionizing dentistry:
Digital Design Process
The process begins with digital impressions or scans of the patient’s oral anatomy using intraoral scanners or cone beam computed tomography (CBCT) imaging. These digital files serve as the foundation for designing dental prostheses and implants using specialized computer-aided design (CAD) software.
Customization and Personalization
One of the key advantages of 3D printing in dentistry is its ability to customize dental devices to each patient’s unique anatomy. Dental professionals can precisely design implants, crowns, bridges, and other prostheses to fit the specific contours of the patient’s teeth and gums, resulting in better fit, comfort, and aesthetics.
Material Selection
3D printing new type of dental implants technology supports a wide range of dental materials, including metals (such as titanium alloys), ceramics, polymers, and composite resins. These materials offer varying degrees of strength, biocompatibility, and esthetics, allowing dental professionals to choose the most suitable material for each patient’s needs.
Layer-by-Layer Fabrication
The 3D printing new type of dental implants process involves the layer-by-layer deposition of material based on the digital design. Depending on the type of 3D printing technology used (e.g., stereolithography, selective laser sintering, fused deposition modeling), the printing process may vary in terms of speed, resolution, and material compatibility.
Post-Processing and Finishing
Once the dental device is printed, it undergoes post-processing steps to remove support structures, polish rough surfaces, and ensure proper fit and alignment. Dental technicians may also apply surface treatments or coatings to enhance biocompatibility, esthetics, and durability.
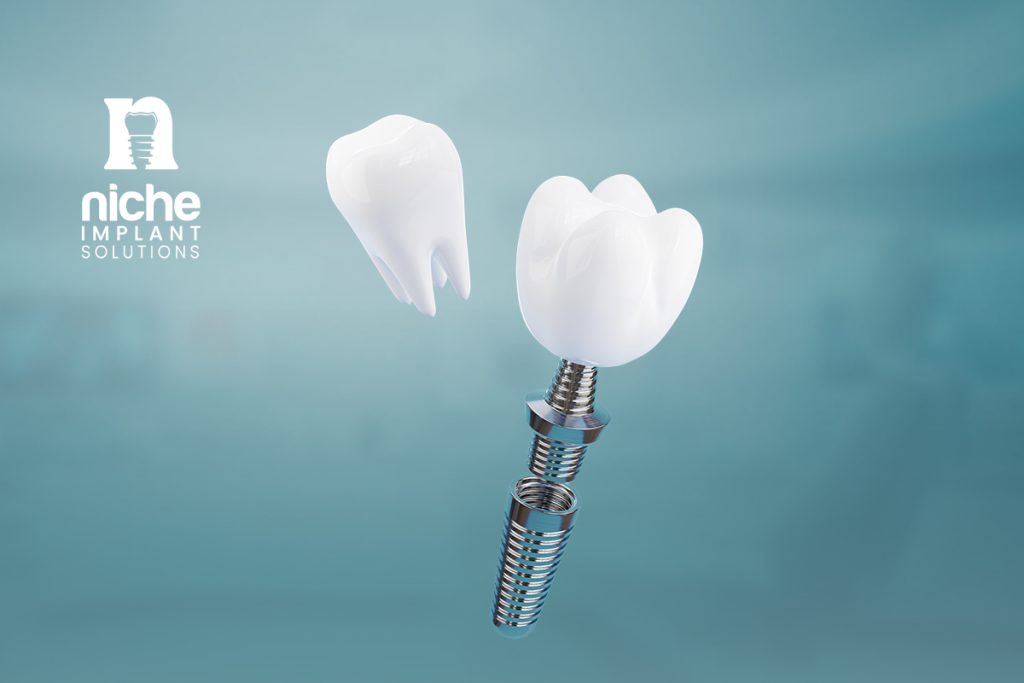
Quality Control and Validation
Quality control measures are essential to ensure the accuracy, reliability, and safety of 3D-printed dental devices. This may involve inspecting printed parts for dimensional accuracy, conducting mechanical testing for strength and durability, and verifying biocompatibility through in vitro and in vivo studies.
Integration with Digital Workflows
In modern dentistry, digital workflows play a central role in streamlining communication, enhancing collaboration, and improving treatment outcomes. Here’s a closer look at how 3D printing technology integrates with digital workflows in dentistry:
- Digital Imaging and Treatment Planning
Digital workflows begin with the acquisition of digital images and diagnostic data, such as intraoral scans, cone beam computed tomography (CBCT) scans, and digital impressions. These digital files provide detailed information about the patient’s oral anatomy and serve as the foundation for treatment planning.
- Virtual Treatment Simulation
Using specialized software, dental professionals can visualize and simulate the proposed treatment plan in a virtual environment. This allows for comprehensive treatment planning, including implant placement, restoration design, and occlusal analysis, before any physical procedures are performed.
- CAD/CAM Design
Once the treatment plan is finalized, dental technicians use computer-aided design (CAD) software to design the dental prostheses, surgical guides, or implants. CAD software offers advanced tools for customizing the shape, size, and fit of the dental devices to match the patient’s unique anatomy.
- Data Transfer and Communication
Digital workflows facilitate seamless communication and data transfer between dental professionals, laboratories, and patients. Digital files can be easily shared and accessed remotely, allowing for real-time collaboration and feedback throughout the treatment process.
- 3D Printing new type of dental implants
Once the digital design is completed, the dental devices are manufactured using 3D printing technology. 3D printers translate the digital designs into physical objects by depositing layers of material according to the specified parameters. This additive manufacturing process enables the rapid production of customized dental devices with high precision and accuracy.
- Post-Processing and Finishing new type of dental implants
After 3D printing new type of dental implants , dental devices undergo post-processing steps to remove support structures, polish rough surfaces, and ensure proper fit and alignment. These finishing touches are essential to achieve the desired aesthetics and functionality of the final prostheses or implants.
- Verification and Validation
Throughout the digital workflow, quality control measures are implemented to verify the accuracy, reliability, and safety of the dental devices. This may involve inspecting printed parts for dimensional accuracy, conducting mechanical testing for strength and durability, and verifying biocompatibility through in vitro and in vivo studies.
Overall, integration with digital workflows enhances efficiency, accuracy, and patient satisfaction in dental practice. By leveraging advanced technologies such as 3D printing, CAD/CAM design, and digital imaging, dental professionals can deliver personalized, high-quality care that meets the unique needs of each patient.
Cost-Effectiveness of 3D-Printed new type of dental implants
In recent years, the field of dentistry has witnessed a paradigm shift with the advent of 3D printing technology. One area where this innovation has had a profound impact is in the fabrication of dental implants. Traditional dental implant systems have long been the gold standard for replacing missing teeth, offering durability, functionality, and aesthetics. However, the introduction of 3D-printed dental implants has raised questions about their cost-effectiveness compared to conventional implants.
Material Usage and Waste Reduction of new type of dental implants
One of the key advantages of 3D-printed new type of dental implants is their efficient use of materials. Unlike traditional implant systems, which often require milling or machining from solid blocks of material, 3D printing technology allows for precise deposition of material only where needed, minimizing waste and maximizing material utilization.
This reduction in material waste can lead to significant cost savings over time, particularly for high-value materials such as titanium alloys or ceramic resins.
Manufacturing Efficiency and Scalability
3D printing new type of dental implants offer inherent advantages in terms of manufacturing efficiency and scalability. Once the digital design is finalized, 3D printers can produce multiple implants simultaneously, with minimal manual intervention and labor costs.
This high degree of automation and repeatability reduces production time and overhead expenses associated with traditional manufacturing processes, resulting in lower overall production costs for 3D-printed dental implants.
Customization and Precision
While the initial setup costs for implementing 3D printing new type of dental implants technology may be higher compared to traditional manufacturing methods, the ability to customize implants to each patient’s unique anatomy can lead to improved treatment outcomes and reduced complications in the long run.
By optimizing implant fit, alignment, and occlusion, 3D-printed dental implants may result in fewer postoperative adjustments, revisions, and associated costs, ultimately enhancing cost-effectiveness over the implant’s lifecycle.
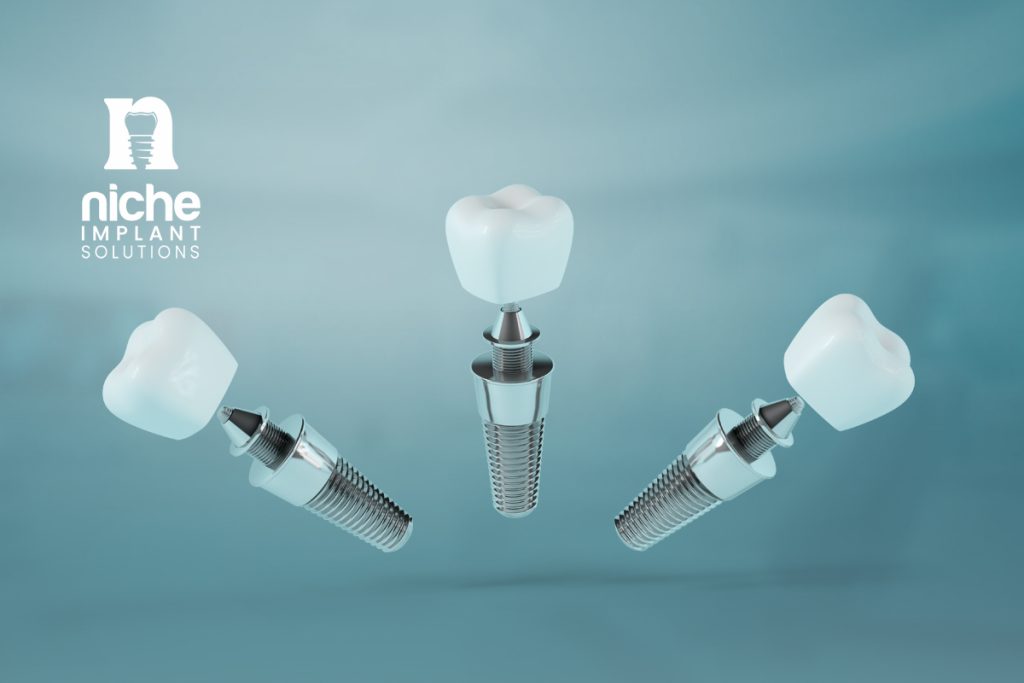
Treatment Efficiency and Patient Satisfaction
Beyond the direct manufacturing costs, 3D-printed new type of dental implants can contribute to overall treatment efficiency and patient satisfaction. The ability to fabricate patient-specific surgical guides enables precise implant placement, minimizing surgical time and reducing the risk of intraoperative complications.
This streamlined approach to treatment can lead to faster healing, reduced chair time, and improved patient comfort, factors that contribute to enhanced patient satisfaction and potentially lower overall treatment costs.
Long-Term Cost Savings and Durability
While the upfront cost of 3D-printed new type of dental implants may be comparable or slightly higher than traditional implants, their long-term cost-effectiveness should also be considered. Studies have shown that 3D-printed implants can exhibit comparable or superior long-term durability and osseointegration compared to conventionally manufactured implants.
By reducing the likelihood of implant failure, complications, and the need for costly revisions or retreatments, 3D-printed dental implants can offer significant cost savings over their lifespan.
Overall, while the cost-effectiveness of 3D-printed new type of dental implants may vary depending on various factors such as material selection, manufacturing processes, and clinical outcomes, they have the potential to offer compelling economic benefits over traditional implant systems.
As technology continues to advance and adoption rates increase, further research and real-world data will provide valuable insights into the true cost-effectiveness of 3D-printed dental implants and their impact on oral healthcare delivery.
Leading the Future: Niche Companies Redefining Dental Implantology with 3D-Printed Solutions new type of dental implants
In conclusion, the emergence of niche companies specializing in 3D-printed dental implants represents a significant advancement in the field of implant dentistry. These companies leverage cutting-edge technology and expertise to provide customized solutions that meet the unique needs of dental professionals and patients alike.
By offering precise implant design, rapid manufacturing, and tailored treatment planning, they have the potential to revolutionize the way dental implants are fabricated and integrated into clinical practice.
Furthermore, niche companies that focus specifically on 3D-printed dental implants demonstrate a commitment to innovation, quality, and patient care.
Their specialized knowledge and experience in additive manufacturing processes enable them to deliver implants of exceptional precision, durability, and biocompatibility. This dedication to excellence not only enhances treatment outcomes but also fosters trust and confidence among dental professionals and patients.
Moreover, niche companies that offer 3D-printed dental implants have the flexibility to adapt quickly to evolving technologies and market demands. By staying at the forefront of advancements in materials science, digital workflows, and regulatory standards, they can continue to push the boundaries of what is possible in implant dentistry.
This dynamic approach ensures that patients receive the most advanced and effective implant solutions available, leading to improved oral health and quality of life.
In summary, niche companies specializing in 3D-printed dental implants play a vital role in driving innovation, improving treatment outcomes, and advancing the field of implant dentistry. Through their commitment to excellence, these companies are reshaping the future of dental implantology and paving the way for a new era of personalized, precision-based dental care.
0 Comments